Historia: La producción de aluminio primario en la Argentina se inició a comienzos de la década del ‘70, dentro de un programa público-privado de desarrollo de la industria del aluminio.
La localidad seleccionada para la instalación de la planta de aluminio primario fue la ciudad de Puerto Madryn, en la Provincia del Chubut, 1.400 Km al sur de la Ciudad Autónoma de Buenos Aires en tanto que la capacidad productiva inicial se estableció en 140.000 toneladas anuales.
En forma simultánea a la construcción de la planta de aluminio primario se llevaron a cabo:
- En Puerto Madryn un puerto de aguas profundas, cuyo objetivo inicial fue facilitar la importación de materias primas para la producción, así como la exportación de metal producido y;
- En Trevelin, a 500 Km al oeste de Puerto Madryn, sobre la Cordillera de los Andes, la Central Hidroeléctrica Futaleufú, para abastecer de energía
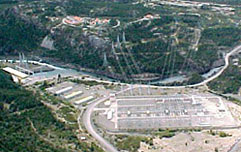
eléctrica a la planta de aluminio.
Este conjunto de emprendimientos constituyó un importante polo de desarrollo regional en la Provincia del Chubut. En efecto, la ciudad de Puerto Madryn, con sólo 6.500 habitantes a comienzos de los '70, supera en la actualidad los 70.000 habitantes.
A meses de la puesta en marcha de la fábrica de aluminio primario, ocurrida en 1974, Aluar comenzó a abastecer totalmente la demanda doméstica de aluminio primario. Desde el inicio
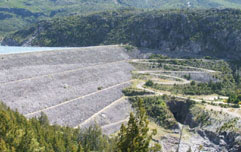
de sus operaciones y con el objetivo de mejorar su posición competitiva, Aluar procuró y alcanzó mejoras productivas de forma permanente y gradual. En lo que refiere al mercado local de productos elaborados de aluminio, el mismo estuvo liderado durante muchos años por Kicsa, del Grupo Aluar, y por Camea, una empresa de la multinacional canadiense Alcan. En 1993 ambos líderes se fusionaron para formar C&K Aluminio S.A., participando en partes iguales en la nueva sociedad. En 1996 Aluar adquirió la totalidad de las acciones de C&K, constituyendo así la División Elaborados de la empresa.
Hacia el año 1998, las instalaciones para solidificación del aluminio líquido en Puerto Madryn fueron ampliadas mediante la compra y posterior fusión por absorción de la empresa Refinería Metales Uboldi, próxima a la planta de aluminio primario. Adicionalmente se realizaron inversiones de actualización tecnológica y ampliación productiva en la empresa así adquirida.
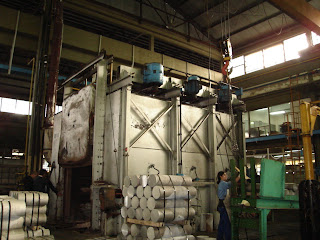
En 1999 con la puesta en marcha de nuevas instalaciones se verificó un salto en sus economías de escala, ampliando un 40% su capacidad productiva de aluminio primario. Las obras requirieron una inversión superior a los 340 millones de dólares. Esta ampliación respondió a una estrategia de reducción del costo de producción y continua actualización tecnológica.
El insumo más importante para la obtención del aluminio es, junto a la alúmina, la energía eléctrica. A efectos de ilustrar tal afirmación basta citar que el consumo de energía eléctrica de una planta de aluminio primario de las dimensiones de la de Aluar en Puerto Madryn equivale al de una ciudad de más de un millón y medio de habitantes.
Aluar entiende que resulta de vital importancia asegurar el abastecimiento de energía eléctrica a su planta. Esta se encuentra localizada, desde el punto de vista eléctrico, en el Sistema Interconectado Patagónico, sistema vinculado a partir de marzo de 2006 con el Sistema Interconectado Nacional.
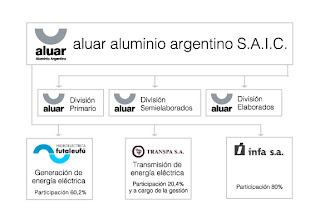
A los efectos de garantizar parte de su abastecimiento, Aluar adquirió en el año 1995 el 59% de las acciones de Hidroeléctrica Futaleufú S.A. (hoy posee el 60,2%), principal generador del sistema patagónico, con una potencia instalada de 472 MW; asimismo posee el 20,4% de TRANSPA S.A., compañía encargada del transporte de energía eléctrica en la región. Esta última empresa opera y mantiene las dos líneas de 330 KV de 550 Km de longitud que vinculan la planta con la central hidroeléctrica Futaleufú.
Aluar posee en su planta equipamiento de generación de energía eléctrica que utiliza gas natural como combustible. En total se disponen de 755 MW, compuestos por dos ciclos combinados de última generación de 585 MW, dos turbinas de gas a ciclo abierto de 40 MW cada una y cuatro turbinas de 22,5 MW. El suministro de gas para las turbinas en condiciones hidrológicas medias, se encuentra asegurado mediante contratos de suministro de largo plazo acordados con productores y con la transportista de gas natural. Con esta
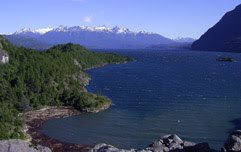
configuración de abastecimiento Aluar logra obtener un abastecimiento confiable de energía eléctrica.
En la División Primario se materializa el grueso de las operaciones de Aluar. Con una capacidad de producción de aluminio primario prevista de 410.000 tn anuales, sus actividades comprenden desde la obtención del aluminio en estado líquido hasta su solidificación en los distintos formatos primarios y aleaciones de acuerdo a los requerimientos específicos de los clientes.
Cuando finalice el proceso de puesta en marcha de la reciente ampliación (a mediados del 2008), la planta productora de aluminio primario tendrá 8 salas que albergarán un total de 712 cubas electrolíticas (hornos en los cuales se obtiene el aluminio
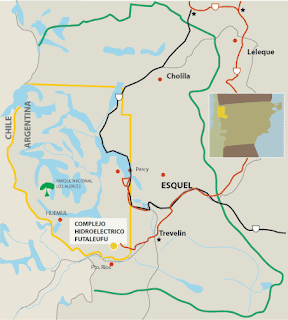
en estado líquido mediante el proceso de electrólisis).
Los requerimientos de energía eléctrica para este proceso están cubiertos por:
-
La Central Hidroeléctrica Futaleufú, con una capacidad instalada de 472 MW y una generación media anual de 2.600.000 Mwh. Posee la concesión por 30 años de la explotación de la represa ubicada sobre el río Grande (Futaleufú) en el noroeste de la Provincia del Chubut, cerca de las ciudades de Esquel y Trevelín, y la propiedad de la central hidroeléctrica. Con una capacidad instalada de 472 Megavatios produce 2900 MWH de energía en condiciones hidrológicas medias. El Complejo Hidroeléctrico fue construido entre 1971 y 1976 e inagurado oficialmente en abril de 1978, habiendo sido proyectado por Agua y Energía Eléctrica Sociedad del Estado de acuerdo a las directivas emanadas por la Comisión Permanente para el Desarrollo de los Metales Livianos (COPEDESMEL), dependiente de la Fuerza Aérea Argentina.
El Complejo fue realizado principalmente con el fin de proveer de energía eléctrica a la planta de aluminio a instalarse en la Ciudad de Puerto Madryn (hoy ALUAR ALUMINIO ARGENTINO S.A.I.C.).
El embalse formado a partir de la construcción de la presa se denomina Amutui Quimei. Este posee una capacidad de almacenaje de 5.700 Hm3 que cubren
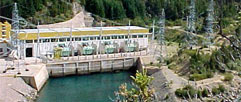
una extensión de 9.200 Ha. La presa está construida de materiales sueltos (tierra o escollera con núcleo de material impermeable), posee una altura de 120 metros, alcanzando la cota de 500 metros sobre el nivel del mar. Su longitud en la parte superior o coronamiento de 600 metros por 10 de ancho se encuentra rematada por un camino ripio consolidado.
El nivel máximo de cota del embalse es de 495 m.s.n.m., dejando un margen de 5 metros hasta la altura límite del muro debido a posibles oleajes y por seguridad de la presa. En la margen derecha de la presa se encuentra el descargador de fondo, este permite el desembalse rápido ante emergencias.
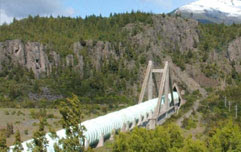
Luego de efectuar un recorrido de 1.895 m por el túnel de aducción y la tubería de presión con un salto máximo de 150 m, el agua alimenta las 4 turbinas Francis de eje vertical de 157 MW, ubicadas en la nave principal del edificio de la Casa de Máquinas, haciéndolas girar transformando la energía potencial en energía mecánica. Sobre el eje de cada una de las turbinas se encuentra vinculado un generador eléctrico de 118 MW en los cuales la energía mecánica es transformada en energía eléctrica.
Una vez cedida su fuerza, el agua es restituida al lecho original del Río Grande (Futaleufú) mediante un corto canal de fuga. Adosada a la Casa de Máquinas se encuentra la playa de transformadores, allí la tensión eléctrica es elevada de 13,8 kV
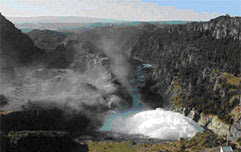
a 330 kV para ser transportada, mediante las líneas de transporte de alta tensión de TRANSPA S.A.
-
Dos centrales térmicas de ciclo combinado de 585 MW de potencia y seis turbinas de gas con una potencia total de 170 MW.
El consumo de energía eléctrica será de aproximadamente 6.000.000 Mwh anuales, equivalente al consumo medio anual de una ciudad de un millón y medio de habitantes.
Aluar cuenta además, con una
fábrica de ánodos (insumo básico requerido por el proceso electrolítico) cuya producción asegura el autoabastecimiento.
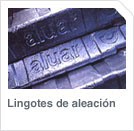
La solidificación del metal se realiza en las instalaciones de fundición que Aluar, con el objetivo de hacer un eficiente uso de los recursos y de diversificación de la producción, ha ido ampliando y perfeccionando a través del tiempo con la creación de su División Semielaborados.
Productos primariosLingote de aleación: Las aleaciones de aluminio primario son una combinación metalúrgica de aluminio y diversos aleantes. Se produce en varias composiciones químicas cumpliendo las especificaciones internacionales existentes. Posee las propiedades características requeridas para la fabricación de piezas por
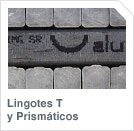
procesos de moldeo. Como ejemplo, se ha desarrollado exitosamente la aleación A356.2, especialmente apta para la producción de llantas de automóviles. El destino de estas aleaciones es principalmente la industria de autopartes.
Lingotes T y prismáticos: Las aleaciones de aluminio primario son una combinación metalúrgica de aluminio y diversos aleantes. El lingote T es un producto fabricado mediante el método de colada continua horizontal, solidificado por enfriamiento directo, lo que le confiere un alto rendimiento en la etapa de refusión. Posee las propiedades características requeridas para la fabricación de piezas por procesos de moldeo. Como ejemplo, se
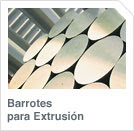
ha desarrollado exitosamente la aleación A356.2, especialmente aptas para la producción de llantas de automóviles. El Lingote Prismático es un producto fabricado mediante el método de colada continua horizontal, solidificado por enfriamiento directo, lo que le confiere un alto rendimiento en la etapa de refusión y posee las mismas características que el anterior. La demanda principal proviene de la industria de autopartes.
Barrotes para extrusión: Es un producto de aleación primaria de aluminio, de forma cilíndrica y dimensiones adecuadas para su posterior transformación mediante el proceso de extrusión. Es fabricado mediante el método de colada semicontinua vertical con tecnología de última generación (Wagstaff Air Slip),
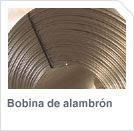
metalúrgicamente homogéneo de acuerdo a normas específicas. Los barrotes son usados en el proceso de extrusión en el que son llevados a alta temperatura y posteriormente sometidos a un severo proceso mecánico de deformación. El destino final de este producto son perfiles de carpintería de aluminio (aberturas, construcción civil, etc), carrocerías de autobuses y camiones, vagones ferroviarios, piezas para coches, bicicletas, piezas para línea blanca, y tubos en general.
Bobina de alambrón: Alambre de aluminio producido por colada y laminación continua en un equipo Properzi, en diámetros comprendidos entre
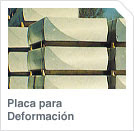
9 y 12 mm (0.35" a 0.47"). Se producen distintas variantes de aluminio puro y con agregado de aleantes. Dada la buena conductibilidad y ventajas en el peso del aluminio con respecto al cobre, es altamente demandado por la industria de conductores eléctricos. Otro de los usuarios son las acerías que lo utilizan en el proceso de desoxidación.
Placa para deformación: Este producto es una placa de aluminio de sección rectangular que posteriormente se procesa en trenes de laminación. La placa es producida por colada semicontinua vertical y solidificación por enfriamiento directo. Se obtiene así una fina estructura de grano que le
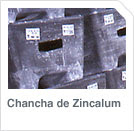
confiere óptimas propiedades para el proceso posterior de laminación en caliente. De este producto se obtienen chapas y láminas para distintos usos tales como menaje, estampados, foils, embalajes, etc.
Chancha de zincalum: La chancha de aleación de zincalum (aleación de 55% aluminio y 45% zinc) se produce por solidificación en moldes de forma apropiada. Es utilizada posteriormente para la generación, por refusión, de un baño de recubrimiento de chapas para la industria de la construcción.
Lingote de aluminio puro: Los principales sectores demandantes de este producto son el de la fundición y el de la industria elaboradora de conductores eléctricos.
Productos laminados:Mediante la fabricación de su amplia gama de productos (perfiles, barras, tubos, laminados gruesos y foil), Aluar División Elaborados provee al mercado materiales de alto valor agregado que satisfacen las necesidades de la industria y la construcción. El adecuado equilibrio de cada una de las líneas y la gran variedad de tipologías brindan al diseñador ilimitadas combinaciones con libertad estética.
Planchas: Las planchas laminadas en caliente son
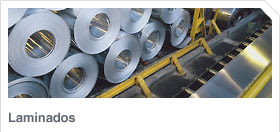
productos laminados planos en altos espesores, que son utilizados donde los requerimientos estructurales son altos. La combinación de resistencia mecánica con un bajo peso específico y una alta resistencia a la corrosión hace que estos productos sean especialmente aptos para la fabricación de maquinaria y para el transporte. Chapas y rollos lisos: Los laminados en frío lisos son productos de espesores medios, que varían entre 0,2 mm y 3 mm La gran versatilidad del aluminio permite usar este tipo de laminados en las más variadas aplicaciones, y en casi todas las industrias conocidas.
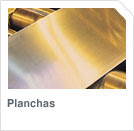
Chapas y rollos gofrados: Los laminados en frío gofrados son productos de espesores medios, que varían entre 0,2 mm y 3 mm, con un acabado superficial que mejora su apariencia exterior y su resistencia mecánica. La gran versatilidad del aluminio permite usar este tipo de laminados en las más variadas aplicaciones, y en casi todas las industrias conocidas.
Foil: El foil de aluminio (o papel de aluminio) consiste en un laminado plano, entregado en rollos, de espesores tan finos que llegan hasta los 6,35 micrones (0,00635 mm.). El uso principal del foil es el packaging de una multitud de productos, especialmente aquellos que necesitan una adecuada barrera a la humedad y a los rayos ultravioletas (como los alimentos o los medicamentos).
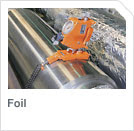
Además, en espesores más altos se puede utilizar para la industria de los bienes de consumo (envases semirígidos), la construcción (membranas asfálticas) o el transporte (radiadores de automóviles).
La
Unidad de Negocio Extrusión División Elaborados, produce una amplia gama de productos que cubren las distintas necesidades tanto del mercado de la construcción como el de la industria.
-Sistemas de carpintería
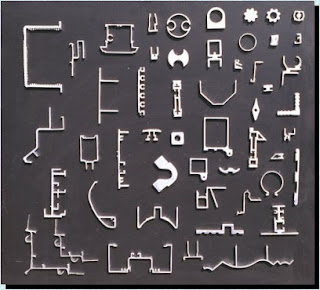
-Perfiles industriales
-Barras trefiladas
El
aluminio es el tercer elemento más abundante en la corteza terrestre y constituye el 7.3% de su masa. En su forma natural, sólo existe en una combinación estable con otros materiales (particularmente en sales y óxidos) y no fue sino hasta 1808 cuando fue descubierto. A partir de entonces, demandó muchos años de investigación y ensayos el poder aislar el aluminio puro del mineral en su estado original, para poder hacer viable su producción, comercialización y procesamiento. De esta manera, el aluminio sólo se produjo para ser comercializado durante el último siglo y medio y es todavía un material muy joven. La humanidad ha utilizado
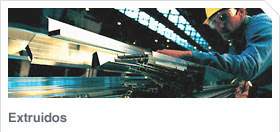
cobre, plomo y estaño por miles de años; sin embargo en la actualidad se produce más aluminio que la suma del resto de la producción de los otros metales no ferrosos. La producción de aluminio primario durante el año 2006 fue de 33.9 millones de toneladas y se prevé crezca a tasas superiores al 5% durante los próximos años.
El aluminio es un material sustentable. Dados los actuales niveles de producción, las reservas conocidas de bauxita –de las cuales se obtiene el mineral de aluminio- durarán por cientos de años. Más del 55% de la
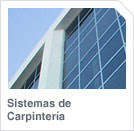
producción mundial de aluminio se realiza utilizando energía hidroeléctrica renovable. Casi la totalidad de los productos de aluminio pueden desde un punto de vista técnico (factibilidad) y económico (rentabilidad) ser reciclados repetidamente para producir nuevos productos, sin perder el metal su calidad y propiedades. La utilización de metales reciclados ahorra energía y preserva las fuentes de recursos naturales. Es por eso que el creciente uso del
aluminio reciclado en diversas aplicaciones le da el reconocimiento de
metal verde.
Proyecto de ampliación de la capacidad productiva de la planta
de aluminio primario en Puerto Madryn
El 24 de junio del 2007 ha comenzado el proceso de puesta en marcha del proyecto de ampliación –Etapa I- de la planta productora de aluminio primario en la ciudad de Puerto Madryn, Provincia del Chubut. Se estima alcanzar el nivel de producción de diseño de esta etapa del proyecto durante el segundo trimestre del año 2008. Con la presencia del Señor Presidente de la Nación y de otras autoridades nacionales, provinciales y municipales, el 3 de septiembre del corriente año, se procedió a la inauguración de las obras –el emprendimiento privado de mayor envergadura llevado a cabo en el país durante los últimos años- que han demandado una inversión de 850 millones de dólares.
El Proyecto
La actual ampliación (etapa I) aumentará la capacidad de producción de aluminio en 137.000 toneladas anuales, alcanzando así un total de 410.000 toneladas. Se cumple de esta forma la primera etapa de un programa de crecimiento orientado a reposicionar a ALUAR en el mercado internacional por incremento de escala y diversificación hacia productos con mayor valor agregado.
La ampliación consistió en las siguientes obras:
- Construcción de dos salas de electrólisis, para albergar una nueva serie (Serie D) de 336 cubas que funcionarán en 220 kA de corriente, instalándose en una primera fase 168 cubas. La producción adicional en términos anuales proporcionada por este primer grupo de cubas es aproximadamente de 105.000 toneladas.
- Aumento de la producción de las Series A y B existentes, a partir del incremento en la intensidad de corriente de las cubas. La producción adicional lograda con esta mejora será de aproximadamente 19.000 toneladas anuales.
- Aumento de la producción de la Serie C existente, a través de la modernización de sus 144 cubas, para poder aumentar la intensidad de corriente en las mismas. La producción lograda con esta transformación será de 13.000 toneladas anuales.
- Instalación de equipamiento de generación consistente en una planta de ciclo combinado de generación de energía eléctrica de 465 MW de capacidad efectiva, sistema de distribución y conversión que cubren los requerimientos de energía eléctrica que demandan los aumentos de producción mencionados.
- Expansión en la planta de ánodos, incorporando un nuevo horno de cocción con su correspondiente planta de tratamiento de humos, modificaciones en el sector molienda y montaje de una nueva línea de varillado de ánodos.
- Instalación de un estación de colada para la solidificación de aluminio líquido en forma de barrotes con una capacidad anual de 80.000 toneladas.
El proyecto se completa con la construcción de diversas instalaciones operativas en las nuevas salas de electrólisis: dos plantas de tratamiento de gases, estaciones de transformación de corriente, y áreas de almacenamiento, además de reemplazo de los grupos rectificadores de energía eléctrica y modificaciones en las actuales cubas electrolíticas en las Series A y B.
La ampliación agrega a la dotación de la planta 250 personas en forma permanente, a las que se le suman el empleo indirecto de aproximadamente 1.000 personas.
La Futura Ampliación.
La futura ampliación de la planta (etapa II) en Puerto Madryn aumentará la producción anual en 105.000 toneladas, destinadas en su totalidad a la exportación. De esta forma la capacidad productiva total del complejo industrial de ALUAR alcanzará las 515.000 toneladas anuales. Este emprendimiento, cuyo plazo de ejecución estimado es de 21 meses, demandará una inversión de 400 millones de dólares y proporcionará empleo durante su construcción a más de 800 personas; luego de su puesta en marcha la dotación de planta aumentará en 180 personas.
LA ACTUAL AMPLIACIÓN, CARACTERÍSTICAS PRINCIPALES
Incremento de producción 137.000 toneladas/año
Incremento de capacidad instalada 50%
Inversión estimada 850 millones de u$s (sin I.V.A.)
Plazo de ejecución de las obras 24 meses
Personal ocupado durante la obra 1500 personas en promedio
6000 personas en el pico de la obra
Destino de la producción Exportación
Incremento de las exportaciones 400 millones u$s/año
Incremento de la Balanza Comercial 270 millones u$s/año
Incremento de dotación en Planta 250 personas
Generación indirecta de empleo 1000 personas
Proyecto realizado bajo el Régimen de Promoción de Inversiones en Bienes de Capital y Obras de Infraestructura.
EL PROYECTO DE LA FUTURA AMPLIACIÓN, CARACTERÍSTICAS PRINCIPALES
Incremento de producción 105.000 toneladas/año
Incremento de capacidad instalada 26%
Inversión estimada 400 millones de u$s (sin I.V.A.)
Destino de la producción Exportación
Incremento de las exportaciones 310 millones u$s/año
Incremento de la Balanza Comercial 210 millones u$s/año
Incremento de dotación en Planta 180 personas con generación indirecta de empleo 700 personas
Fuente: Aluar on line e Internet.